1. General
Aircraft type training shall consist of theoretical training and examination, and, except for the category C ratings, practical training and assessment.
(a) Theoretical training and examination shall comply with the following requirements:
(i) Shall be conducted by a maintenance training organisation appropriately approved in accordance with Annex IV (Part-147) or, when conducted by other organisations, as directly approved by the competent authority.
(ii) Shall comply, except as permitted by the differences training provided for in point (c), with the standard set out in point 3.1 of this Appendix and, if available, the relevant elements defined in the mandatory part of the operational suitability data established in accordance with Regulation (EU) No 748/2012.
(iii) In the case of a category C person qualified by holding an academic degree as specified in point 66.A.30(a)(5), the first relevant aircraft type theoretical training shall be at the category B1 or B2 level.
(iv) Shall have been started and completed within the 3 years preceding the application for a type rating endorsement.
(b) Practical training and assessment shall comply with the following requirements:
(i) Shall be conducted by a maintenance training organisation appropriately approved in accordance with Annex IV (Part-147) or, when conducted by other organisations, as directly approved by the competent authority.
(ii) Shall comply, except as permitted by the differences training described in point (c), with the standard set out in point 3.2 of this Appendix and, if available, the relevant elements defined in the mandatory part of the operational suitability data established in accordance with Regulation (EU) No 748/2012.
(iii) Shall include a representative cross section of maintenance activities relevant to the aircraft type.
(iv) Shall include demonstrations using equipment, components, simulators, other training devices or aircraft.
(v) Shall have been started and completed within the 3 years preceding the application for a type rating endorsement.
(c) Differences training
(i) Differences training is the training required in order to cover the differences between two different aircraft type ratings of the same manufacturer as determined by the Agency.
(ii) Differences training has to be defined on a case-to-case basis taking into account the requirements contained in this Appendix III in respect of both theoretical and practical elements of type rating training.
(iii) A type rating shall only be endorsed on a licence after differences training when the applicant also complies with one of the following conditions:
— having already endorsed on the licence the aircraft type rating from which the differences are being identified, or
— having completed the type training requirements for the aircraft from which the differences are being identified.
AMC to Paragraph 1(c) of Appendix III to Part-66 ‘Aircraft Type Training and Examination Standard. On-the-Job Training’
Differences Training
Approved difference training is not required for different variants within the same aircraft type rating (as specified in Appendix I to AMC to Part-66) for the purpose of type rating endorsement on the aircraft maintenance licence.
However, this does not necessarily mean that no training is required before a certifying staff authorisation can be issued by the maintenance organisation (refer to AMC 66.A.20(b)3).
AMC to Section 1 of Appendix III to Part-66 ‘Aircraft Type Training and Examination Standard. On-the-Job Training’
Aircraft Type Training
1. Aircraft type training may be sub-divided in airframe and/or powerplant and/or avionics/electrical systems type training courses.
— Airframe type training course means a type training course including all relevant aircraft structure and electrical and mechanical systems excluding the powerplant.
— Powerplant type training course means a type training course on the bare engine, including the build-up to a quick engine change unit.
— The interface of the engine/airframe systems should be addressed by either airframe or powerplant type training course. In some cases, such as for general aviation, it may be more appropriate to cover the interface during the airframe course due to the large variety of aircraft that can have the same engine type installed.
— Avionics/electrical systems type training course means type training on avionics and electrical systems covered by but not necessarily limited to ATA (Air Transport Association) Chapters 22, 23, 24, 25, 27, 31, 33, 34, 42, 44, 45, 46, 73 and 77 or equivalent.
2. Practical training may be performed either following or integrated with the theoretical elements. However, it should not be performed before theoretical training.
3. The content of the theoretical and practical training should:
— address the different parts of the aircraft which are representative of the structure, the systems/components installed and the cabin; and
— include training on the use of technical manuals, maintenance procedures and the interface with the operation of the aircraft.
Therefore it should be based on the following elements:
— Type design including relevant type design variants, new technology and techniques;
— Feedback from in-service difficulties, occurrence reporting, etc;
— Significant applicable airworthiness directives and service bulletins;
— Known human factor issues associated with the particular aircraft type;
— Use of common and specific documentation, (when applicable, such as MMEL, AMM, MPD, TSM, SRM, WD, AFM, tool handbook), philosophy of the troubleshooting, etc.;
— Knowledge of the maintenance on-board reporting systems and ETOPS maintenance conditions where applicable;
— Use of special tooling and test equipment and specific maintenance practises including critical safety items and safety precautions;
— Significant and critical tasks/aspects from the MMEL, CDL, Fuel Tank Safety (FTS), airworthiness limitation items (ALI) including Critical Design Configuration Control Limitations (CDCCL), CMR and all ICA documentation such as MRB, MPD, SRM, AMM, etc., when applicable.
— Maintenance actions and procedures to be followed as a consequence of specific certification requirements, such as, but not limited to, RVSM (Reduced Vertical Separation Minimum) and NVIS (Night Vision Imaging Systems);
— Knowledge of relevant inspections and limitations as applicable to the effects of environmental factors or operational procedures such as cold and hot climates, wind, moisture, sand, de-icing / anti-icing, etc.
The type training does not necessarily need to include all possible customer options corresponding to the type rating described in the Appendix I to AMC to Part-66.
4. Limited avionic system training should be included in the category B1 type training as the B1 privileges include work on avionics systems requiring simple tests to prove their serviceability.
5. Electrical systems should be included in both categories of B1 and B2 type training.
6. The theoretical and practical training should be complementary and may be:
— Integrated or split
— Supported by the use of training aids, such as trainers, virtual aircraft, aircraft components, synthetic training devices (STD), computer based training devices (CBT), etc.
2. Aircraft type training levels
The three levels listed below define the objectives, the depth of training and the level of knowledge that the training is intended to achieve.
— Level 1: A brief overview of the airframe, systems and powerplant as outlined in the Systems Description Section of the Aircraft Maintenance Manual/Instructions for Continued Airworthiness.
Course objectives: Upon completion of Level 1 training, the student will be able to:
(a) provide a simple description of the whole subject, using common words and examples, using typical terms and identify safety precautions related to the airframe, its systems and powerplant;
(b) identify aircraft manuals, maintenance practices important to the airframe, its systems and powerplant;
(c) define the general layout of the aircraft’s major systems;
(d) define the general layout and characteristics of the powerplant;
(e) identify special tooling and test equipment used with the aircraft.
— Level 2: Basic system overview of controls, indicators, principal components, including their location and purpose, servicing and minor troubleshooting. General knowledge of the theoretical and practical aspects of the subject.
Course objectives: In addition to the information contained in the Level 1 training, at the completion of Level 2 training, the student will be able to:
(a) understand the theoretical fundamentals; apply knowledge in a practical manner using detailed procedures;
(b) recall the safety precautions to be observed when working on or near the aircraft, powerplant and systems;
(c) describe systems and aircraft handling particularly access, power availability and sources;
(d) identify the locations of the principal components;
(e) explain the normal functioning of each major system, including terminology and nomenclature;
(f) perform the procedures for servicing associated with the aircraft for the following systems: Fuel, Power Plants, Hydraulics, Landing Gear, Water/Waste, and Oxygen;
(g) demonstrate proficiency in use of crew reports and on-board reporting systems (minor troubleshooting) and determine aircraft airworthiness per the MEL/CDL;
(h) demonstrate the use, interpretation and application of appropriate documentation including instructions for continued airworthiness, maintenance manual, illustrated parts catalogue, etc.
— Level 3: Detailed description, operation, component location, removal/installation and bite and troubleshooting procedures to maintenance manual level.
Course objectives: In addition to the information contained in Level 1 and Level 2 training, at the completion of Level 3 training, the student will be able to:
(a) demonstrate a theoretical knowledge of aircraft systems and structures and interrelationships with other systems, provide a detailed description of the subject using theoretical fundamentals and specific examples and to interpret results from various sources and measurements and apply corrective action where appropriate;
(b) perform system, powerplant, component and functional checks as specified in the aircraft maintenance manual;
(c) demonstrate the use, interpret and apply appropriate documentation including structural repair manual, troubleshooting manual, etc.;
(d) correlate information for the purpose of making decisions in respect of fault diagnosis and rectification to maintenance manual level;
(e) describe procedures for replacement of components unique to aircraft type.
3. Aircraft type training standard
Although aircraft type training includes both theoretical and practical elements, courses can be approved for the theoretical element, the practical element or for a combination of both.
3.1 Theoretical element
(a) Objective:
On completion of a theoretical training course the student shall be able to demonstrate, to the levels identified in the Appendix III syllabus, the detailed theoretical knowledge of the aircraft’s applicable systems, structure, operations, maintenance, repair, and troubleshooting according to approved maintenance data. The student shall be able to demonstrate the use of manuals and approved procedures, including the knowledge of relevant inspections and limitations.
(b) Level of training:
Training levels are those levels defined in point 2 above.
After the first type course for category C certifying staff all subsequent courses need only be to level 1.
During a level 3 theoretical training, level 1 and 2 training material may be used to teach the full scope of the chapter if required. However, during the training the majority of the course material and training time shall be at the higher level.
(c) Duration:
The theoretical training minimum tuition hours are contained in the following table:
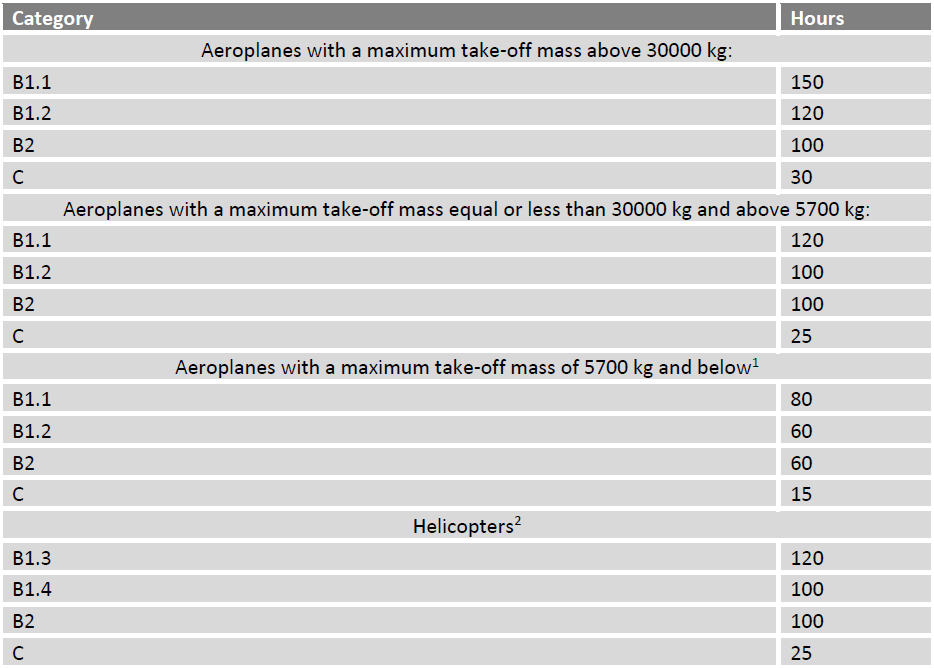
For the purpose of the table above, a tuition hour means 60 minutes of teaching and exclude any breaks, examination, revision, preparation and aircraft visit.
These hours apply only to theoretical courses for complete aircraft/engine combinations according to the type rating as defined by the Agency.
(d) Justification of course duration:
Training courses carried out in a maintenance training organisation approved in accordance with Annex IV (Part-147) and courses directly approved by the competent authority shall justify their hour duration and the coverage of the full syllabus by a training needs analysis based on:
— the design of the aircraft type, its maintenance needs and the types of operation,
— detailed analysis of applicable chapters — see contents table in point 3.1(e) below,
— detailed competency analysis showing that the objectives as stated in point 3.1(a) above are fully met.
Where the training needs analysis shows that more hours are needed, course lengths shall be longer than the minimum specified in the table.
Similarly, tuition hours of differences courses or other training course combinations (such as combined B1/B2 courses), and in cases of theoretical type training courses below the figures given in point 3.1(c) above, these shall be justified to the competent authority by the training needs analysis as described above.
In addition, the course must describe and justify the following:
— The minimum attendance required to the trainee, in order to meet the objectives of the course.
— The maximum number of hours of training per day, taking into account pedagogical and human factors principles.
If the minimum attendance required is not met, the certificate of recognition shall not be issued. Additional training may be provided by the training organisation in order to meet the minimum attendance time.
AMC to point 3.1(d) of Appendix III to Part-66 ‘Aircraft Type Training and Examination Standard. On-the-Job Training’
Training Needs Analysis for the Theoretical Element of the Aircraft Type Training
1. The minimum duration for the theoretical element of the type rating training course, as described in Appendix III to Part-66, has been determined based on:
— generic categories of aircraft and minimum standard equipment fit
— the estimated average duration of standard courses imparted in Europe
2. The purpose of the Training Needs Analysis (TNA) is to adapt and justify the duration of the course for a specific aircraft type. This means that the TNA is the main driver for determining the duration of the course, regardless of whether it is above or below the minimum duration described in Appendix III to Part-66.
In the particular case of type training courses approved on the basis of the requirements valid before Regulation (EU) No 1149/2011 was applicable (1 August 2012) and having a duration for the theoretical element equal to or above the minimum duration contained in paragraph 3.1(c) of Appendix III to Part-66, it is acceptable that the TNA only covers the differences introduced by Regulation (EU) No 1149/2011 in paragraph 3.1(e) ‘Content’ and the criteria introduced in paragraph 3.1(d) ‘Justification of course duration’ related to the minimum attendance and the maximum number of training hours per day. This TNA may result in a change in the duration of the theoretical element.
3. The content and the duration deriving from this TNA may be supported by an analysis from the Type Certificate holder.
4. In order to approve a reduction of such minimum duration, the evaluation done by the competent authority should be performed on a case-by-case basis appropriate to the aircraft type. For example, while it would be exceptional for a theoretical course for a transport category complex motor-powered aircraft such as an A330 or B757 to be below the minimum duration shown, it would not necessarily be exceptional in the case of a General Aviation (GA) business aircraft such as a Learjet 45 or similar. Typically the TNA for a GA aircraft course would demonstrate that a course of a shorter duration satisfies the requirements.
5. When developing the TNA the following should be considered:
(a) The TNA should include an analysis identifying all the areas and elements where there is a need for training as well as the associated learning objectives, considering the design philosophy of the aircraft type, the operational environment, the type of operations and the operational experience. This analysis should be written in a manner which provides a reasonable understanding of which areas and elements constitute the course in order to meet the learning objectives.
(b) As a minimum, the Training Need Analysis (TNA) should take into account all the applicable elements contained in paragraph 3.1 of Part-66 Appendix III and associated AMCs.
(c) The TNA should set-up the course content considering the Appendix III objectives for each level of training and the prescribed topics in the theoretical element table contained in paragraph 3.1 of Part-66 Appendix III.
(d) For each chapter described in the theoretical element table contained in paragraph 3.1 of Part-66 Appendix III, the corresponding training time should be recorded.
(e) Typical documents to be used in order to identify the areas and elements where there is a need for training typically include, among others, the Aircraft Maintenance Manual, MRB report, CMRs, airworthiness limitations, Troubleshooting Manual, Structural Repair Manual, Illustrated Parts Catalogue, Airworthiness Directives and Service Bulletins.
(f) During the analysis of these documents:
— Consideration should be given to the following typical activities:
— Activation/reactivation;
— Removal/Installation;
— Testing;
— Servicing;
— Inspection, check and repairs;
— Troubleshooting / diagnosis.
— For the purpose of identifying the specific elements constituting the training course, it is acceptable to use a filtering method based on criteria such as:
— Frequency of the task;
— Human factor issues associated to the task;
— Difficulty of the task;
— Criticality and safety impact of the task;
— In-service experience;
— Novel or unusual design features (not covered by Part-66 Appendix I);
— Similarities with other aircraft types;
— Special tests and tools/equipment.
— It is acceptable to follow an approach based on:
— Tasks or groups of tasks, or
— Systems or subsystems or components
(g) The TNA should:
— Identify the learning objectives for each task, group of tasks, system, subsystem or component;
— Associate the identified tasks to be trained to the regulatory requirements (table in Paragraph 3.1 of Appendix III to Part-66);
— Organise the training into modules in a logical sequence (adequate combination of chapters as defined in Appendix III of Part-66);
— Determine the sequence of learning (within a lesson and for the whole syllabus);
— Identify the scope of information and level of detail with regard the minimum standard to which the topics of the TNA should be taught according to the set-up objectives.
— Address the following:
— Description of each system/component including the structure (where applicable);
— System/component operation taking into account:
(a) Complexity of the system (e.g. the need of further break down into subsystems, etc.);
(b) Design specifics which may require more detailed presentation or may contribute to maintenance errors;
(c) Normal and emergency functioning;
(d) Troubleshooting;
(e) Interpretation of indications and malfunctions;
(f) Use of maintenance publications;
(g) Identification of special tools and equipment required for servicing and maintaining the aircraft;
(h) Maintenance Practices;
(i) Routine inspections, functional or operational tests, rigging/adjustment, etc.
— Describe the following:
— The instructional methods and equipment, teaching methods and blending of the teaching methods in order to ensure the effectiveness of the training;
— The maintenance training documentation/material to be delivered to the student;
— Facilitated discussions, questioning session, additional practiced-oriented training, etc.;
— The homework, if developed;
— The training provider’s resources available to the learner.
(h) It is acceptable to differentiate between issues which have to be led by an instructor and issues which may be delivered through interactive simulation training devices and/or covered by web based elements. Overall time of the course will be allocated accordingly.
(i) The maximum number of training hours per day for the theoretical element of type training should not be more than 6 hours. A training hour means 60 minutes of tuition excluding any breaks, examination, revision, preparation and aircraft visit. In exceptional cases, the competent authority may allow deviation from this standard when it is properly justified that the proposed number of hours follows pedagogical and human factors principles. These principles are especially important in those cases where:
— Theoretical and practical training are performed at the same time;
— Training and normal maintenance duty/apprenticeship are performed at the same time.
(j) The minimum participation time for the trainee in order to meet the objectives of the course should not be less than 90 % of the tuition hours of the theoretical training course. Additional training may be provided by the training organisation in order to meet the minimum participation time. If the minimum participation defined for the course is not met, a certificate of recognition should not be issued.
(k) The TNA is a living process and should be reviewed/updated based on operation feedback, maintenance occurrences, airworthiness directives, major service bulletins impacting maintenance activities or requiring new competencies for mechanics, alert service bulletins, feedback from trainees or customer satisfaction, evolution of the maintenance documentation such as MRBs, MPDs, MMs, etc. The frequency at which the TNA should be reviewed/updated is left to the discretion of the organisation conducting the course.
NOTE: The examination is not part of the TNA. However, it should be prepared in accordance with the learning objectives described in the TNA.
(e) Content:
As a minimum, the elements in the Syllabus below that are specific to the aircraft type shall be covered. Additional elements introduced due to type variations, technological changes, etc. shall also be included.
The training syllabus shall be focused on mechanical and electrical aspects for B1 personnel, and electrical and avionic aspects for B2.
Note 1: For non-pressurised piston engine aeroplanes below 2 000 kg MTOM, the minimum duration can be reduced by 50 %.
Note 2: For helicopters in Group 2 (as defined in point 66.A.5), the minimum duration can be reduced by 30 %.
(f) Multimedia Based Training (MBT) methods may be used to satisfy the theoretical training element either in the classroom or in a virtual controlled environment subject to the acceptance of the competent authority approving the training course.
3.2 Practical element
(a) Objective:
The objective of practical training is to gain the required competence in performing safe maintenance, inspections and routine work according to the maintenance manual and other relevant instructions and tasks as appropriate for the type of aircraft, for example troubleshooting, repairs, adjustments, replacements, rigging and functional checks. It includes the awareness of the use of all technical literature and documentation for the aircraft, the use of specialist/special tooling and test equipment for performing removal and replacement of components and modules unique to type, including any on-wing maintenance activity.
(b) Content:
At least 50 % of the crossed items in the table below, which are relevant to the particular aircraft type, shall be completed as part of the practical training.
Tasks crossed represent subjects that are important for practical training purposes to ensure that the operation, function, installation and safety significance of key maintenance tasks is adequately addressed; particularly where these cannot be fully explained by theoretical training alone. Although the list details the minimum practical training subjects, other items may be added where applicable to the particular aircraft type.
Tasks to be completed shall be representative of the aircraft and systems both in complexity and in the technical input required to complete that task. While relatively simple tasks may be included, other more complex tasks shall also be incorporated and undertaken as appropriate to the aircraft type.
Glossary of the table: LOC: Location; FOT: Functional/Operational Test; SGH: Service and Ground Handling; R/I: Removal/Installation; MEL: Minimum Equipment List; TS: TroubleShooting.
(b) The incorrect alternatives shall seem equally plausible to anyone ignorant of the subject. All the alternatives shall be clearly related to the question and of similar vocabulary, grammatical construction and length.
(c) In numerical questions, the incorrect answers shall correspond to procedural errors such as the use of incorrect sense (+ versus -) or incorrect measurement units. They shall not be mere random numbers.
(d) The level of examination for each chapter1 shall be the one defined in point 2 ‘Aircraft type training levels’. However, the use of a limited number of questions at a lower level is acceptable.
(e) The examination shall be of the closed book type. No reference material is permitted. An exception will be made for the case of examining a B1 or B2 candidate’s ability to interpret technical documents.
(f) The number of questions shall be at least 1 question per hour of instruction. The number of questions for each chapter and level shall be proportionate to:
— the effective training hours spent teaching at that chapter and level,
— the learning objectives as given by the training needs analysis.
The competent authority of the Member State will assess the number and the level of the questions when approving the course.
(g) The minimum examination pass mark is 75 %. When the type training examination is split in several examinations, each examination shall be passed with at least a 75 % mark. In order to be possible to achieve exactly a 75 % pass mark, the number of questions in the examination shall be a multiple of 4.
(h) Penalty marking (negative points for failed questions) is not to be used.
(i) End of module phase examinations cannot be used as part of the final examination unless they contain the correct number and level of questions required.
4.2. Practical element assessment standard
After the practical element of the aircraft type training has been completed, an assessment must be performed, which must comply with the following:
(a) The assessment shall be performed by designated assessors appropriately qualified.
(b) The assessment shall evaluate the knowledge and skills of the trainee.
AMC to Paragraphs 1(b), 3.2 and 4.2 of Appendix III to Part-66 ‘Aircraft Type Training and Examination Standard. On-the-Job Training’
Practical Element of the Aircraft Type Training
1. The practical training may include instruction in a classroom or in simulators but part of the practical training should be conducted in a real maintenance or manufacturer environment.
2. The tasks should be selected because of their frequency, complexity, variety, safety, criticality, novelty, etc. The selected tasks should cover all the chapters described in the table contained in paragraph 3.2 of Appendix III to Part-66.
3. The duration of the practical training should ensure that the content of training required by paragraph 3.2 of Appendix III to Part-66 is completed.
Nevertheless, for aeroplanes with a MTOM equal or above 30000kg, the duration for the practical element of a type rating training course should not be less than two weeks unless a shorter duration meeting the objectives of the training and taking into account pedagogical aspects (maximum duration per day) is justified to the competent authority.
4. The organisation providing the practical element of the type training should provide trainees a schedule or plan indicating the list of tasks to be performed under instruction or supervision. A record of the tasks completed should be entered into a logbook which should be designed such that each task or group of tasks may be countersigned by the designated assessor. The logbook format and its use should be clearly defined.
5. In paragraph 4.2 of Appendix III to Part-66, the term ‘designated assessors appropriately qualified’ means that the assessors should demonstrate training and experience on the assessment process being undertaken and be authorised to do so by the organisation.
Further guidance about the assessment and the designated assessors is provided in Appendix III to AMC to Part-66.
6. The practical element (for powerplant and avionic systems) of the Type Rating Training may be subcontracted by the approved Part-147 organisation under its quality system according to the provisions of 147.A.145(d)3 and the corresponding Guidance Material.
5. Type examination standard (Appendix III to Part-66)
Type examination shall be conducted by training organisations appropriately approved under Part-147 or by the competent authority.
The examination shall be oral, written or practical assessment based, or a combination thereof and it shall comply with the following requirements:
(a) Oral examination questions shall be open.
(b) Written examination questions shall be essay type or multi-choice questions.
(c) Practical assessment shall determine a person’s competence to perform a task.
Note: For the purpose of this point 4, a ‘chapter’ means each one of the rows preceded by a number in the table contained in point 3.1(e).
(d) Examinations shall be on a sample of chapters1 drawn from point 3 type training/examination syllabus, at the indicated level.
(e) The incorrect alternatives shall seem equally plausible to anyone ignorant of the subject. All of the alternatives shall be clearly related to the question and of similar vocabulary, grammatical construction and length.
(f) In numerical questions, the incorrect answers shall correspond to procedural errors such as corrections applied in the wrong sense or incorrect unit conversions: they shall not be mere random numbers.
(g) The examination shall ensure that the following objectives are met:
1. Properly discuss with confidence the aircraft and its systems.
2. Ensure safe performance of maintenance, inspections and routine work according to the maintenance manual and other relevant instructions and tasks as appropriate for the type of aircraft, for example troubleshooting, repairs, adjustments, replacements, rigging and functional checks such as engine run, etc., if required.
3. Correctly use all technical literature and documentation for the aircraft.
4. Correctly use specialist/special tooling and test equipment, perform removal and replacement of components and modules unique to type, including any on-wing maintenance activity
(h) The following conditions apply to the examination:
1. The maximum number of consecutive attempts is three. Further sets of three attempts are allowed with a 1 year waiting period between sets. A waiting period of 30 days is required after the first failed attempt within one set, and a waiting period of 60 days is required after the second failed attempt.
The applicant shall confirm in writing to the maintenance training organisation or the competent authority to which they apply for an examination, the number and dates of attempts during the last year and the maintenance training organisation or the competent authority where these attempts took place. The maintenance training organisation or the competent authority is responsible for checking the number of attempts within the applicable timeframes.
2. The type examination shall be passed and the required practical experience shall be completed within the 3 years preceding the application for the rating endorsement on the aircraft maintenance licence.
3. Type examination shall be performed with at least one examiner present. The examiner(s) shall not have been involved in the applicant’s training.
(i) A written and signed report shall be made by the examiner(s) to explain why the candidate has passed or failed.
Note 1: For the purpose of this point 5, a ‘chapter’ means each one of the rows preceded by a number in the tables contained in points 3.1(e) and 3.2(b).
AMC to Section 5 of Appendix III to Part-66 ‘Aircraft Type Training and Examination Standard. On-the-Job Training’
Type Examination Standard
This Section 5 ‘Type Examination Standard’ does not apply to the examination performed as part of type training. This Section only applies to those cases where type examination is performed as a substitute for type training.
6. On the Job Training
On the Job Training (OJT) shall be approved by the competent authority who has issued the licence.
It shall be conducted at and under the control of a maintenance organisation appropriately approved for the maintenance of the particular aircraft type and shall be assessed by designated assessors appropriately qualified.
It shall have been started and completed within the 3 years preceding the application for a type rating endorsement.
(a) Objective:
The objective of OJT is to gain the required competence and experience in performing safe maintenance.
(b) Content:
OJT shall cover a cross section of tasks acceptable to the competent authority. The OJT tasks to be completed shall be representative of the aircraft and systems both in complexity and in the technical input required to complete that task. While relatively simple tasks may be included, other more complex maintenance tasks shall also be incorporated and undertaken as appropriate to the aircraft type.
Each task shall be signed off by the student and countersigned by a designated supervisor.
The tasks listed shall refer to an actual job card/work sheet, etc.
The final assessment of the completed OJT is mandatory and shall be performed by a designated assessor appropriately qualified.
The following data shall be addressed on the OJT worksheets/logbook:
1. Name of Trainee;
2. Date of Birth;
3. Approved Maintenance Organisation;
4. Location;
5. Name of supervisor(s) and assessor, (including licence number if applicable);
6. Date of task completion;
7. Description of task and job card/work order/tech log, etc.;
8. Aircraft type and aircraft registration;
9. Aircraft rating applied for.
In order to facilitate the verification by the competent authority, demonstration of the OJT shall consist of (i) detailed worksheets/logbook and (ii) a compliance report demonstrating how the OJT meets the requirement of this Part.
AMC to Section 6 of Appendix III to Part-66 ‘Aircraft Type Training and Examination Standard. On-the-Job Training’
On-the-Job Training (OJT)
- ‘A maintenance organisation appropriately approved for the maintenance of the particular aircraft type’ means a Part-145, M.A. Subpart F or Part-CAO approved maintenance organisation holding an A rating for such aircraft.
- The OJT should include one to one supervision and should involve actual work task performance on aircraft/components, covering line and/or base maintenance tasks.
- The use of simulators for OJT should not be allowed.
- The OJT should cover at least 50% of the tasks contained in Appendix II to AMC to Part-66. Some tasks should be selected from each paragraph of the Appendix II list. Tasks should be selected among those applicable to the type of aircraft and licence (sub)category applied for. Other tasks than those in the Appendix II may be considered as a replacement when they are relevant. Typically, in addition to the variety and the complexity, the OJT tasks should be selected because of their frequency, safety, novelty, etc.
- Up to 50% of the required OJT may be undertaken before the aircraft theoretical type training starts.
- The organisation providing the on-the-job training should provide trainees a schedule or plan indicating the list of tasks to be performed under supervision. A record of the tasks completed should be entered into a logbook which should be designed such that each task or group of tasks is countersigned by the corresponding supervisor. The logbook format and its use should be clearly defined.
- Regarding the day-to-day supervision of the OJT programme in the approved maintenance organisation and the role of the supervisor(s), the following should be considered:
— It is sufficient that the completion of individual OJT tasks is confirmed by the direct supervisor(s), without being necessary the direct evaluation of the assessor.
— During the day-to-day OJT performance, the supervision aims at overseeing the complete process, including task completion, use of manuals and procedures, observance of safety measures, warnings and recommendations and adequate behaviour in the maintenance environment.
— The supervisor(s) should personally observe the work being performed to ensure the safe completeness and should be readily available for consultation, if needed during the OJT performance.
— The supervisor(s) should countersign the tasks and release the maintenance tasks as the trainee is still not qualified to do so.
— The supervisor(s) should therefore:
— have certifying staff or support staff privileges relevant to the OJT tasks;
— be competent for the selected tasks;
— be safety-orientated;
— be capable to coach (setting objectives, giving training, performing supervision, evaluating, handling trainee’s reactions and cultural issues, managing objectively and positively debriefing sessions, determining the need for extra training or reorientate the training, reporting, etc.);
— be designated by the approved maintenance organisation to carry out the supervision. - Regarding the assessor, the following should be considered:
— The function of the assessor, as described in Section 6 of Appendix III to Part-66, is to conduct the final assessment of the completed OJT. This assessment should include confirmation of the completion of the required diversity and quantity of OJT and should be based on the supervisor(s) reports and feedback.
— In Section 6 of Appendix III to Part-66, the term ‘designated assessor appropriately qualified’ means that the assessor should demonstrate training and experience on the assessment process being undertaken and should be authorised to do so by the organisation. Further guidance about the assessment and the designated assessors is provided in Appendix III to AMC to Part-66. - The procedures for OJT of a Part-145 organisation should be included into the Exposition Manual of the approved maintenance organisation (chapter 3.15, as indicated in AMC 145.A.70(a)).
However, since these procedures are approved by the competent authority of the maintenance organisation, and providing training is not one of the privileges of a maintenance organisation, they can only be used when the licensing authority is the same as the competent authority of the maintenance organisation. In other cases, it is up to the licensing authority to decide whether it accepts such procedures for the purpose of approving the OJT (refer to AMC 66.B.115).
AMC to Appendix III to Part-66 ‘Aircraft Type Training and Examination Standard. On-the-Job Training’
Aircraft Type Training and On-the-Job Training
The theoretical and practical training providers, as well as the OJT provider, may contract the services of a language translator in the case where training is imparted to students not conversant in the language of the training material. Nevertheless, it remains essential that the students understand all the relevant maintenance documentation.
During the performance of examinations and assessments, the assistance of the translator should be limited to the translation of the questions, but should not provide clarifications or help in relation to those questions.